Surfer Tom Cooke stands on a beach in Encinitas where other surfers are catching plenty of waves. It’s a nice clean beach but plastic waste isn’t far away, floating in what’s called the Pacific Garbage Patch.
Go elsewhere in the world to surf, Cooke said, and you see a lot more stuff washed up on the beaches.
“In El Salvador, it was a big rock beach with a lot of tidal flow. There was someone coming everyday to pick up plastic bottles and flip flops. And they were trying to clean it but it was just a constant flow of plastics,” he said. “I mean, this stuff was piled up like mid-shin in El Salvador. It was pretty gross.”
Cooke isn’t just a surfer. He’s president of a company called Blueview Footwear that makes biodegradable sneakers. Cooke knows the business of recreational footwear well, having worked for Reef and Vans.
The science behind these shoes comes from Stephen Mayfield, Blueview's CEO and UC San Diego distinguished professor of molecular biology.
At Mayfield's lab, pieces of the foam material that go into Blueview sneakers swirl in vials of liquid as they sit on a gently moving platform. The water is filled with tiny ocean organisms that are invited to consume the material.
“As we’re degrading our foams we’re also trying to isolate the organisms that biodegrade them,” Mayfield said.
Biodegradable plastics that go into Blueview shoes are made from algae oil. Mayfield said it’s ironic that ancient deposits of algae oil have become the petroleum that are mined for normal plastics.
“Super simple, right? It was like … plastics come from petroleum. Petroleum comes from algae. Let’s make plastics directly from algae,” he said.
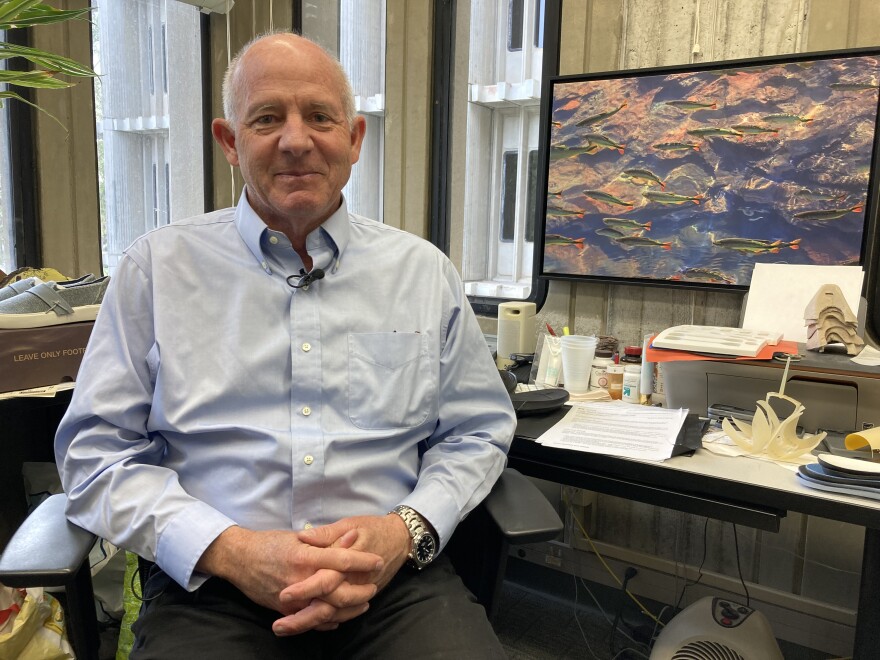
Mayfield said scientists 70 years ago could have created plastics that degrade and return to the earth. But in an effort to make something very durable, they didn’t foresee the problem with the plastic waste stream that is now so obvious.
“So when we set about to redevelop these things, we said ‘let's make plastics from algae but let’s make plastics that biodegrade at the end of their lives.’ The material has a half-life that is proportional to the product,” Mayfield said.
Based on Blueview's experiments, the shoes will fully degrade in soil and compost in about nine months. In the ocean, it can take two years.
Why plastic recycling hasn’t succeeded
The U.S. has tried to make plastic recycling work for more than 30 years. It hasn't had the results that some hoped for.
In 2018, the U.S. Environmental Protection Agency (EPA) estimated that the plastic recycling rate was 8.7%. Since then the plastics industry itself has reported that plastic recycling has declined. A recent Greenpeace report estimated only about 5% of household plastics are recycled in the U.S.
Mayfield calls the promise of plastic recycling "hooey." The many varieties of plastic, usually contaminated with food or soda, make recycling the material difficult to impossible.
“(Let’s say) you had a plastic water bottle and it cost you a penny to make it. Then you put Coke in it. You have to wash it out before you recycle it, and it’s going to cost you a lot more than a penny, and then the water to wash it out. So that’s why (plastic) recycling never works,” he said.
The San Diego company Geno, once called Genomatica, has been bioengineering plant-based plastics for more than 20 years. Company CEO Christophe Schilling, who got his Ph.D. at UC San Diego, said plastic recycling is possible. But it requires a clean, pure stream of the same kind of plastic.
That’s not what you find in a San Diego recycling bin.
“To be relying on plastic recycling as the solution to our plastic waste challenges … It can be part of the solution but we need to come up with other alternative approaches,” Schilling said.
Getting petroleum out of the picture
Geno-produced materials, derived from plants, go into making nylon for apparel. Other products are used to formulate cosmetics.
Schilling said making the plastic materials out of plants instead of petroleum reduces carbon emissions in the production process by 90%. A primary building block for Geno's bioplastic products is sugar. Corn kernels, for instance, are packed with sugar.
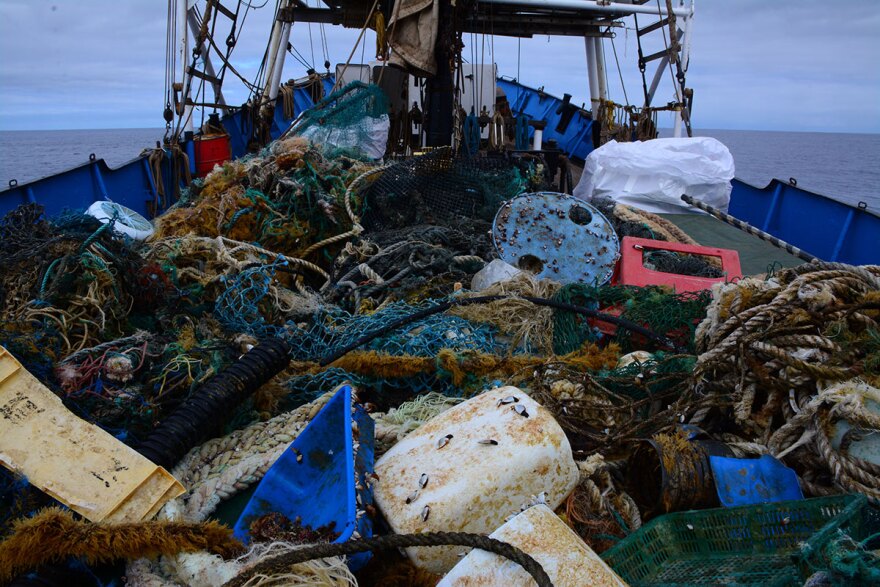
“Our technology is being used today at the core of a $300 million capital project to build a manufacturing facility in Iowa,” Schilling said. “It will take corn, produced by American farmers, and convert that into materials that we’ll find in a range of different products.”
Geno technology is being used to make biodegradable plastic bags at a plant in Italy. But many of the plastic materials Geno makes from plants do not degrade. The nylon they make is no different chemically from those that are made from petroleum.
Schilling said it's unrealistic to say we can phase out non-degradable plastics in the making of all products.
“For example, the plastic parts that are in your car or in your cell phone or in your computer,” he said. “The area of concern is more what you would think of as single-use products. That’s what generates waste.”
Blueview Footwear’s Mayfield said he would never make a boat hull, which is constantly exposed to water, out of degradable plastic. “But equally it’s kind of silly to make plastics that are going to last for a thousand years, then put that into a car that might last 20,” he said.
Meanwhile, consumers and governments have choices to make when it comes to the future of plastic. In a new California law signed last year, grocers must provide compostable pre-checkout bags — the kind used for meat and produce — by 2025.
-
Republicans are still grappling over who will lead their party — the U.S. House of Representatives is still without a Speaker after voting over two days.
-
Plastic products have become a huge environmental problem and some San Diego companies are trying to change that by creating new kinds of plastics.