On the western edge of Scripps Ranch, just off I-15, construction crews are assembling a 10-story building made entirely out of wood. But the building won't ever be inhabited — in fact, crews will be tearing it down next year.
That's because the building, officially called the NHERI Tall Wood Project, is an experiment co-sponsored by the UC San Diego School of Engineering. It has been built to test an emerging construction material called mass timber.
Mass timber is created by joining multiple planks of wood, often with glue, to form large panels and beams that can be used to construct buildings up to 18 stories high, thanks to recent updates to the California building code.
The material is considered much more climate-friendly in high-rise buildings because unlike steel or concrete, which require large amounts of energy to produce, mass timber comes from a renewable resource grown by the sun.
Trees capture carbon from the atmosphere through photosynthesis and store it in their cells, meaning the production of mass timber can help mitigate the burning of fossil fuels. Mass timber can also be produced with small-diameter trees and those affected by disease, insects or wildfires.
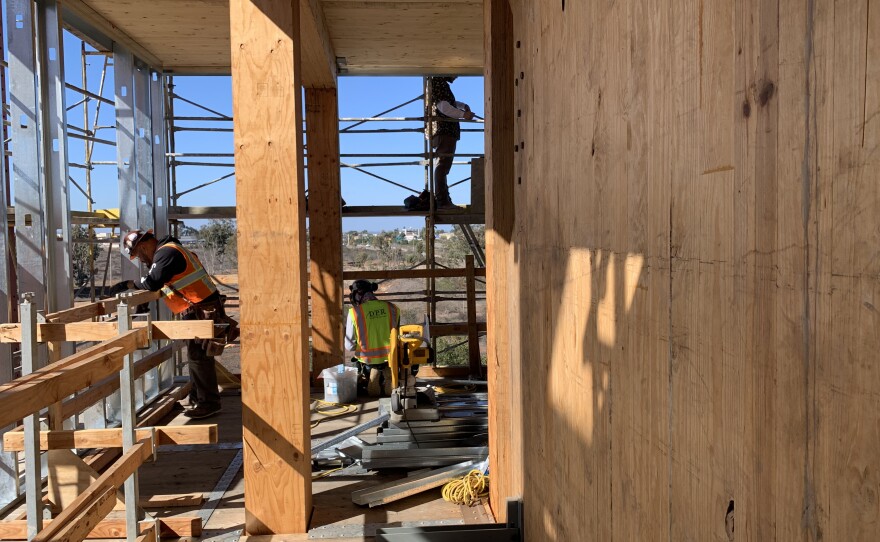
San Diego's recently updated Climate Action Plan briefly mentions mass timber as a less carbon-intensive building material that the city should seek to incentivize, though exactly what those incentives might look like or when they would be adopted is unclear.
Jennifer Cover, president and CEO of WoodWorks, a nonprofit that promotes mass timber, said architects and engineers have long struggled with how to produce large buildings more sustainably.
"(Mass timber) will revolutionize the way we build," Cover said. "The building industry contributes about 40% of the total greenhouse gasses globally. And if you just look at building materials alone, it's somewhere between 9 to 11%."
The mass timber test building in Scripps Ranch, which sits on a large platform called a shake table, will be built with walls that are designed to move and absorb energy during earthquakes. Come February, the shake table will mimic multiple earthquakes with growing intensity. Dozens of sensors in the building will produce data that show how the shaking impacts the building's structural integrity.
Shiling Pei, a professor of engineering at the Colorado School of Mines who is leading the experiment, said he expects the building will see little if any structural damage.
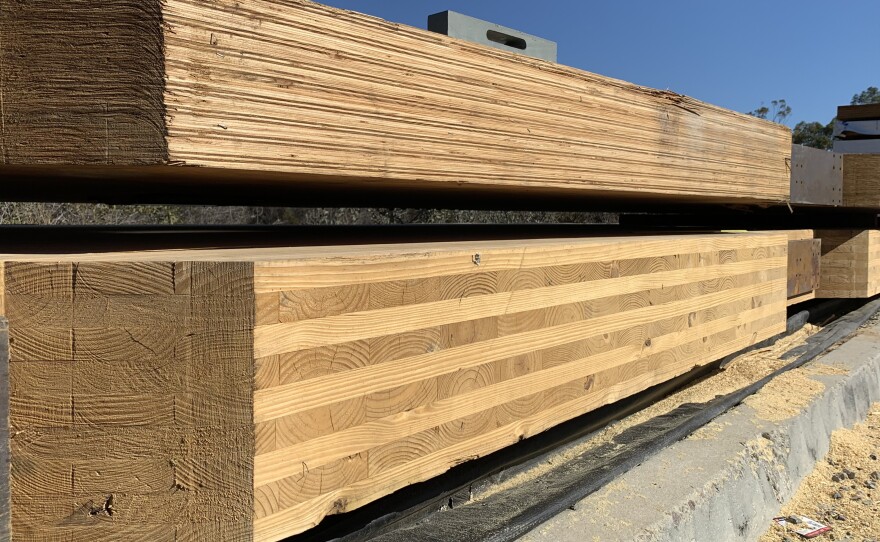
"The reason we do tests is we don't know the full story," Pei said. "In a way, we're playing a role to be a good educator for the public and building officials to say this is totally feasible, and there's a great benefit if you're ever going to encounter a huge earthquake."
Past research into mass timber has shown it's also remarkably resilient to fire. Since mass timber panels are many times thicker than conventional two-by-fours, they can be exposed to fire for hours with only charring on the outside.
"What that does is create an insulation layer against further heat damage," Cover said. "So the wood is actually protected and it self-extinguishes."
Despite the growing popularity of mass timber in North America, it remains a novelty for most developers in San Diego. But some are beginning to incorporate it into their projects in small ways.
Alexander Alemany leads Hub & Spoke Communities, a local small-scale development firm that plans to use mass timber floors and ceilings in a five-story apartment building on El Cajon Boulevard in North Park. The walls will be made out of conventional wood framing.
"We wanted to understand this new building material and methodology first, so that's why we did a hybrid approach," Alemany said.
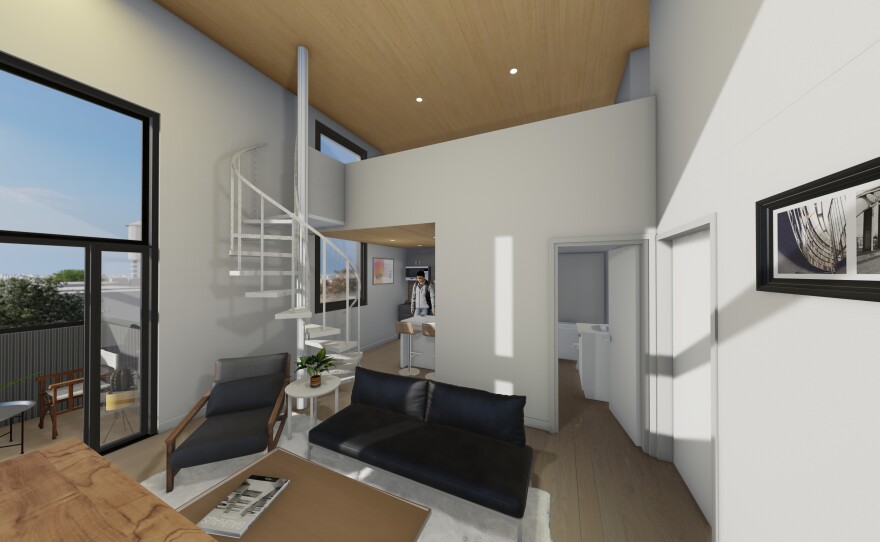
Mass timber is 15 to 25% more expensive than typical wood, Alemany said, and he'll have to offset those costs with higher rents — which he hopes people will pay for the warm, inviting feel of exposed wood in their homes. But because mass timber panels can be produced offsite to the specifications of each individual building, construction can take place much faster and with fewer people.
Still, the supply of contractors who have experience with mass timber is still very limited in San Diego. Alemany said he expects it will take more large, institutional development firms to get on board before the material becomes truly mainstream.
"The more and more of those larger-scale projects that get accomplished with mass timber, there's going to be a trickle down effect to the mass market and smaller projects," Alemany said.
Beyond the development community, the city of San Diego also needs to get more comfortable with mass timber, said Alemany's business partner, Jake Cattanach. The team submitted its plans to the city's Development Services Department in December 2021 and is hoping for a building permit by the end of the year.
"They put a very inexperienced reviewer on (our project)," Cattanach said. "The city has not been easy to deal with."