From the quirky to the quaint, the vogue of wearing hats has been a mainstay at horse races around the world. When it comes to opening day in Del Mar, Jill Courtemanche said San Diegans don’t think about their head fashion until after the July 4th holiday.
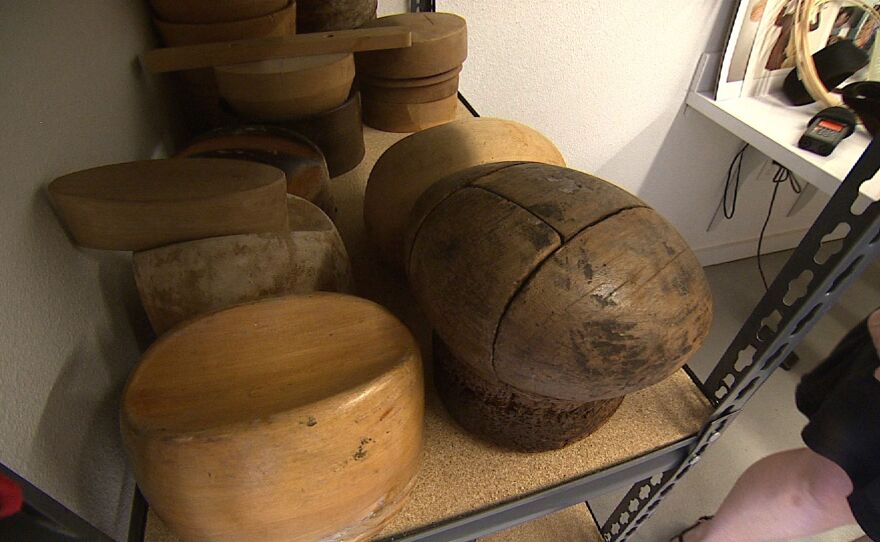
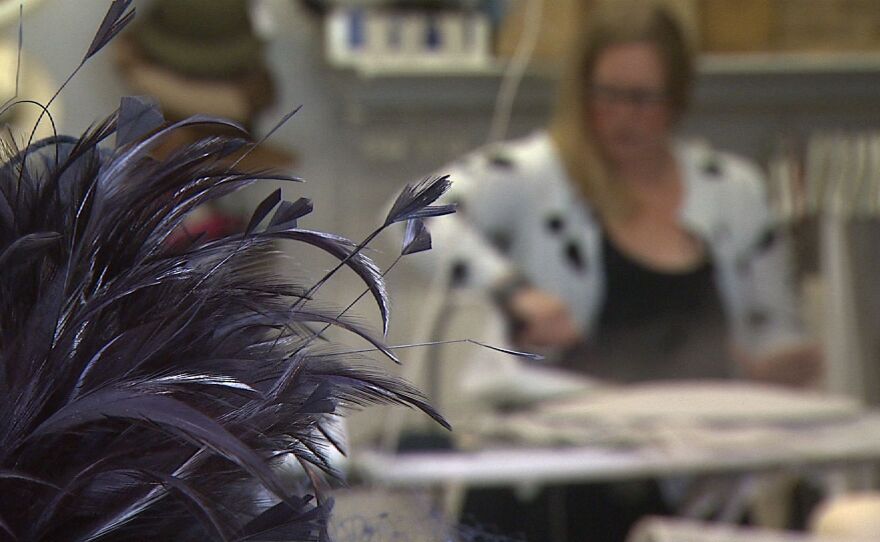
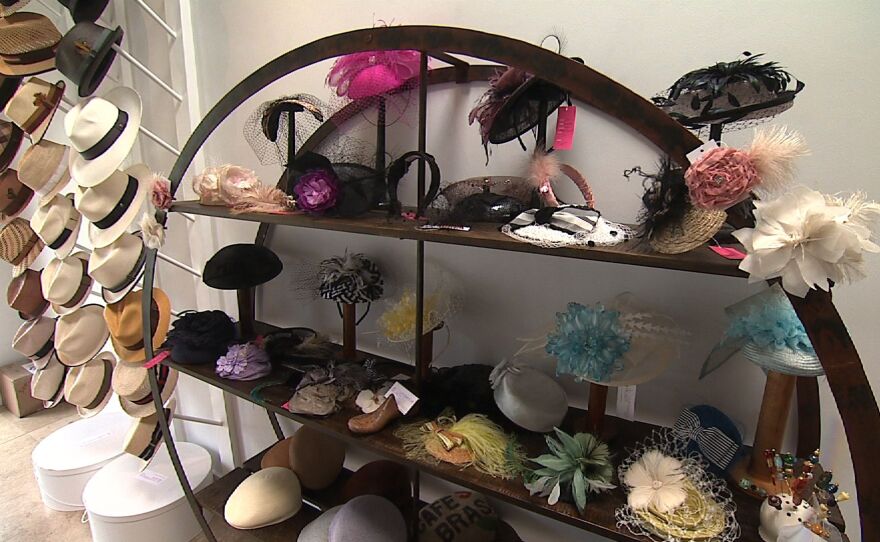
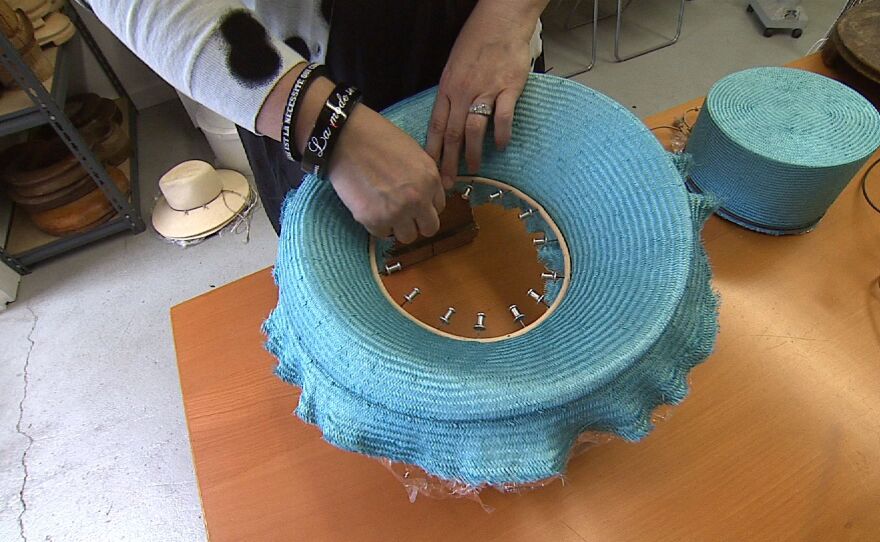
“We are literally here all night long the night before, and people are stopping by to pick up their hats as they drive down the street to the racetrack,” she said.
Local hat maker, or milliner, Jill Courtemanche uses longstanding techniques passed down through decades of millinery to create headdresses for the modern age. She attended the Fashion Institute in New York, and went on to study under influential milliners who taught her traditional methods for creating hats.
"There used to be a milliner on every street corner," she said. "It was as ubiquitous as nail salons and pizza parlors are today."
Sometimes she gets lucky and finds treasures long forgotten. Recently she came across bags full of Ecuadorian raw straws that had been stored and long forgotten by someone in San Diego.
"It’s hard to believe they had been sitting in someone’s garage for over 10 years," she said.
Preserved with the perfect amount of moisture to keep them supple, Courtemanche said these straws are of exceptional quality and are very hard to find because they are not made at this level anymore.
Panamas are graded by the fineness of their weave; the tighter the weave, the lighter the hat. The tightest weave of all is a Montecristi, which can cost up to $2,000.
Courtemanche uses wooden forms, or hat blocks, to create the foundation for her hats. Like a photographic negative, the molds are used to reproduce hat shapes that are then embellished with trimming.
The hat blocks are made from balsa or hardwood and are all carved by hand.
"They can cost up to $1,000 or more, it just depends how intricate the detailing is," Courtemanche said.
There are only a few time-honored custom block shapers left in the world. New and vintage blocks are stamped, indicating where they are made and the maker who made them.
"When they’re designed, they actually put newspaper in between [the wood] for it to dry," she said.
The newspaper print often transfers onto the wood, "so you can also get a little history lesson on what was popular at the time," she said. "Once in a while you can see a date on them."
As fashions change, some trends are left to history, while others enjoy waves of resurgence. The practice of wearing hats may have changed through the ages but, as Courtemanche illustrates, the craft of millinery remains tried and true.