With the popularity of 3-D printers growing, San Diego State University students are getting the chance to create products and start their own businesses before they even graduate. And those efforts will grow starting in January, when SDSU opens a 3-D printing studio in the Love Library. It’ll be available to all students, and they can print anything they want, within reason.
What You Can't Print
Material that is:
- prohibited by local, state or federal law;
- unsafe, harmful, dangerous or poses an immediate threat to the well-being of others (such use may violate the terms of use of the manufacturer);
- obscene or otherwise inappropriate for the library environment;
- in violation of another’s intellectual property rights (For example, the printers will not be used to reproduce material that is subject to copyright, patent or trademark protection.)
“Having that exposure gives them a competitive edge. It can also inspire them to think about projects and develop entrepreneurial kinds of thinking,” said Gale Etschmaier, SDSU’s library dean.
Students in San Diego want that edge. And 3-D printing can give it to them by yielding fast, inexpensive results, making new products, or valuable prototypes, in minutes.
Mark Figueroa, SDSU library’s head of digital initiatives, said the project will start with a small studio but could grow as students pick up 3-D skills.
The first studio will have at least one printer — a MakerBot — and an upscale computer with 3-D compatible software. Desktop MakerBot printers cost around $3,000. The project included an additional $2,000 for maintenance. It’s paid for by the library’s student use fee.
“To get the program going, students will experiment with printing objects that have already been designed — a cellphone case for example. They can go in and print these things and see how it works,” Figueroa said.
He said the next step is designing objects from scratch. This aspect of the technology is harder to master. Many online forums offer predesigned 3-D objects to download, including cellphone cases. Figueroa said designing any 3-D object requires time and expertise, so more computers and space will probably be needed in the future.
“We hope this will be a small workshop where students who are really interested in designing their own types of products can come in and learn how to use the software and design their own products. And this may be in conjunction with the Zahn center on campus,” Figueroa said.
The Zahn Innovation Center is a wing of a small IT building. The main workspace inside is open and bright, with colorful new furniture. It includes two meeting rooms and a workshop. One room has two microwave-sized 3-D printers along the wall. The workshop in the back has an industrial-grade printer, about the size of a mini fridge.
The 3-D printer fires up with a surprising amount of noise – it sounds like a paper printer from the 1990s. The printer pulls from a spool of thin plastic wire and feeds it through the printer head that works like a hot glue gun, quickly melting then hardening the plastic.
The Zahn center is where engineering student Spencer Koroly started his own business. He’s making protective gear for extreme sports.
“I ran around campus interviewing everyone I saw holding a skateboard and asked them their experience with safety equipment,” Koroly said.
He then had to have his business plan vetted and accepted by the center’s director. Once that happened, Koroly could start making his prototypes for protective gear.
“It’s a high performance, low-profile kneepad for skateboarding and other action sports. The goal is to create a product that is low profile that still offers enough protection and flexibility where people will actually want to wear the safety equipment,” Koroly said.
Koroly’s protective gear company is called Manis because the parts mimic the scales of the manis pangolin, an animal that looks like an artichoke with a tail.
Right now the company is building prototypes using the 3-D printer. Koroly and his team create life-size representations of their experimental gear quickly and cheaply at the Zahn center.
Koroly makes all his designs from scratch using a software program called Solidworks. It’s a program used for general engineering design but also saves in formats required for 3-D printers. After he saves his new design in the proper file-type, he plugs the memory card into the printer and starts it up.
It melts the plastic to near-liquid form to take the proper shape for Manis pads, then quickly cools in place. In minutes, the Manis team has a new prototype ready to test. Koroly can pull these parts straight from the printer bed and test them out on the street. They’re not as durable as the final product will be, but they’re good enough to test and display.
Without the Zahn center’s 3-D printers, he would have to make parts out of metal and plastic scraps. “I would have to go through a much lengthier manufacturing process for prototyping. So I’d spend more time prototyping something that probably won’t work than I will actually working on the design and evolving it. So having the 3-D printer allows me to use a more complicated design and make those prototypes much faster,” Koroly said.
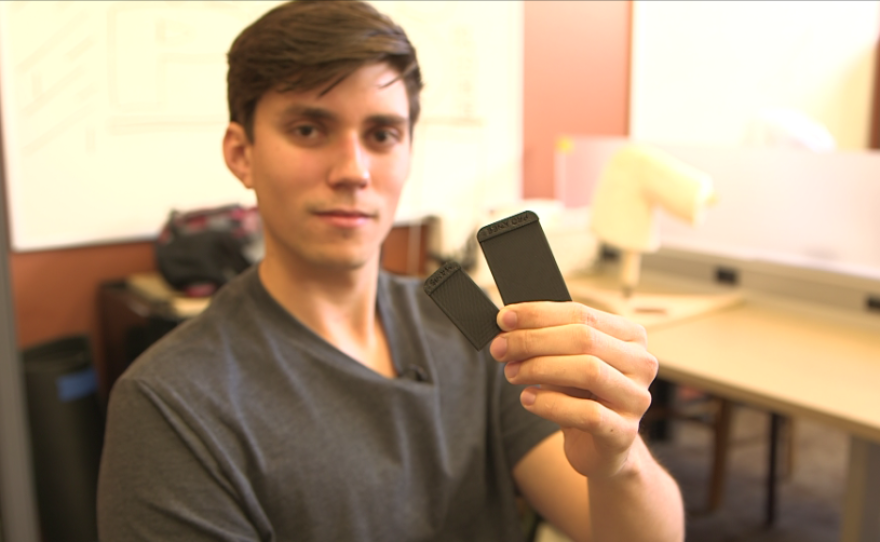
Since the Zahn center accepted his project in March 2014, Koroly has grown Manis to six staffers, including himself. They’re focusing all their efforts on an online fundraising campaign through Kickstarter.
SDSU engineering student Jennifer Wood is also working from the Zahn center to establish a business. Wood and her team are using 3-D printers to test prototype parts for a 3-D printer of their own. Yes, she’s making a 3-D printer with a 3-D printer.
Her team is also developing user friendly 3-D software for smartphones and tablets.
Etschmaier, the library dean, said the biggest drive behind SDSU’s 3-D workshop is speeding up student success. Other student entrepreneurs have told her, “If you had a 3-D printer in the library, we could have brought our product to market much faster.”